Rebecca joined Jaguar Land Rover on the Graduate Engineering Programme after completing a degree in Mechanical Engineering and going on to do a Masters in Materials Engineering.
She is incredibly passionate about her work and has been able to bring together her expertise and experience in materials engineering with her interest in making materials more sustainable.
We asked her to share her experiences here at JLR heading up a large team of Materials Engineers at a time where Jaguar Land Rover is transforming to be able to meet its sustainability goals.
Tell us a bit about your team and what they do.
The Materials Engineering team is made up of just over 100 people, with 11 managers covering all materials. The team provides specialist technical leadership and consultancy service to the whole business, including material investigations, selection and specification advice, material testing and analysis, material technology research and developments for new products. We have Labs in Gaydon, Castle Bromwich and Whitley and work very closely with our materials suppliers.
Our work is critical to our business strategy since the engineering community is responsible for scope 3 upstream emissions, which make up a large proportion of our indirect emissions, therefore the work that we do will have a large impact on meeting our 2030 SBTI targets. We are working to address CO2, provenance, circularity and hazardous materials.
What do you love most about your job?
I love that my job is so varied, so for example yesterday I was in the design studio talking about the materials we were going to be using on our next generation platform, this‑morning I have been in conversations about improving the sustainability credentials of metals, this‑afternoon will be focussed on how we are including sustainability materials in our CAD systems. The content and the people I work with are really varied.
You have worked for Jaguar Land Rover in this area for 15 years. How has it changed during that time from a sustainability point of view?
There has been a huge shift in attitudes and working practices when it comes to material selection since I first started. I was one of the original team working on the pioneering REALCAR project. Working in a team of 4 in the lab and hand in hand with Novelis, a leading aluminum supplier, we succeeded in creating a new chemistry for Aluminium, which meant we could use over 50% recycled aluminum content in our car bodies.
The REALCAR project was the very first look into life cycle assessment (LCA). Now LCA is fully embedded into our engineering culture – it’s extremely important for us as a business and critical to meeting our science‑based target commitments.
That project also closed the loop on the waste aluminium in our press shops. Typically 50% of the aluminium used in the stamping process is not utilised but we are able to work with our internal press shops and supplier press shops to turn that all back into sheet aluminum for reuse.
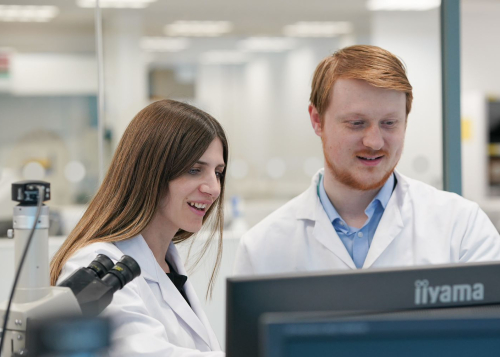
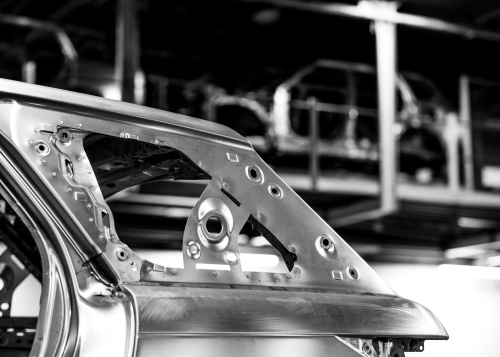
What materials are the most challenging in terms of recycled content or recyclability?
I would say for us polymers are very challenging. When recycled, polymers usually get darker – many recycled polymers are black. From a design perspective, particularly modern luxury – the trend is towards lighter coloured materials so this can be very difficult to create.
For metals, recycled castings can be more tolerant. Sheet metal is more challenging because of the manufacturing processes both at the supplier (e.g. rolling) our in‑house process (stamping and joining).
Can you give any insights into what you are working on now or what future projects might look like?
There needs to be more recycled content in everything we produce. We can’t have linear models anymore – we have to transition to a circular approach. So in the future we want all aluminum grades to have high recycled content including post‑consumer content. And it’s not just aluminum – glass, rubber, steel and polymers – we are looking at all materials in our products from this perspective.
Materials also have to be recyclable at end‑of‑life, so we are working to ensure we build that into material design. For example, ensuring interior parts that are wrapped have a compatible chemistry with the substrate they are wrapped to, so that they can be recycled easily at end of life without having to be segregated. This also demonstrates how recyclability has to be a consideration during the design phase.
Reducing the amount of materials used is the number one way to reduce CO2, followed by selecting less impactful material, and finally by lowering the impact of that material by increasing recycled content.
Ultimately, in the future we want to be refining and recycling value from waste rather than mining new materials.